Original Post Date : 4/19/23
How do you know you're really getting the best product available? For this post we spoke with Matt, a member of our inspection team. Through his valuable insights, we gained an understanding of why Midwest Tungsten Service is recognized for delivering products of superior quality.
Why is having an inspection team important at MTS?
Having an inspection team ensures high standards for our products. We want to get it right. We really value repeat business, which is why accuracy is of the upmost importance. We truly care about our customers, so we want to do our job right to help them succeed.
What are some of the protocols used to help maintain such high product quality for your customers?
MTS is ISO certified. We hold ourselves accountable to the highest quality standards throughout the entire company. For instance, we don't just assume that when a part comes out of the machine shop that it is correct. While our machinists are consummate professionals, we think it makes sense to have a set of independent eyes review the part against the print before we ship. While not every job actually requires that we have ISO certification or this level of inspection, we provide it because we believe that it is the right thing to do.
If there was one word that would be associated with the Inspection team, what would it be?
Accuracy, that is what inspection is all about. At MTS, we use state-of-the-art inspection equipment that ensures accuracy of our measurements. We regularly calibrate that equipment to established standards to make sure our measurements are correct, reliable, and accurate.
What type of Machines/Instruments are used by Inspection that has helped build product trust and reliability for MTS?
In addition to the standard micrometers and calipers that you might find in most machine shops, we have a number of CMMs (Coordinate Measurement Machines) of both the touch probe and optical inspection type. Some of these devices can take measurements during a machining operation without even removing the part from the machine. We have a Profilometer to measure the surface finish of a part. We also have ultrasound inspection, magnetic susceptibility (mu) measuring equipment, and lots of other measuring equipment. Occasionally, we will send a part out for a very specific type of inspection that we don't have the capacity to perform ourselves.
Is there another service the MTS Inspection team provides that your customers may not know about?
Yes, we sometimes make custom fixturing or inspection equipment, if necessary, to get the job done correctly. The inspection team also provides input to the shipping department as to how to best package an item to avoid damage during shipping. We want parts to arrive to the customer as a perfect as when we inspected them here.
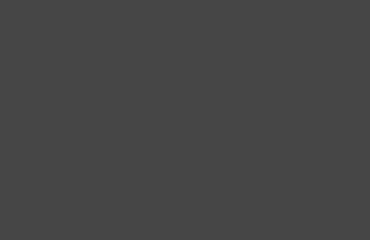